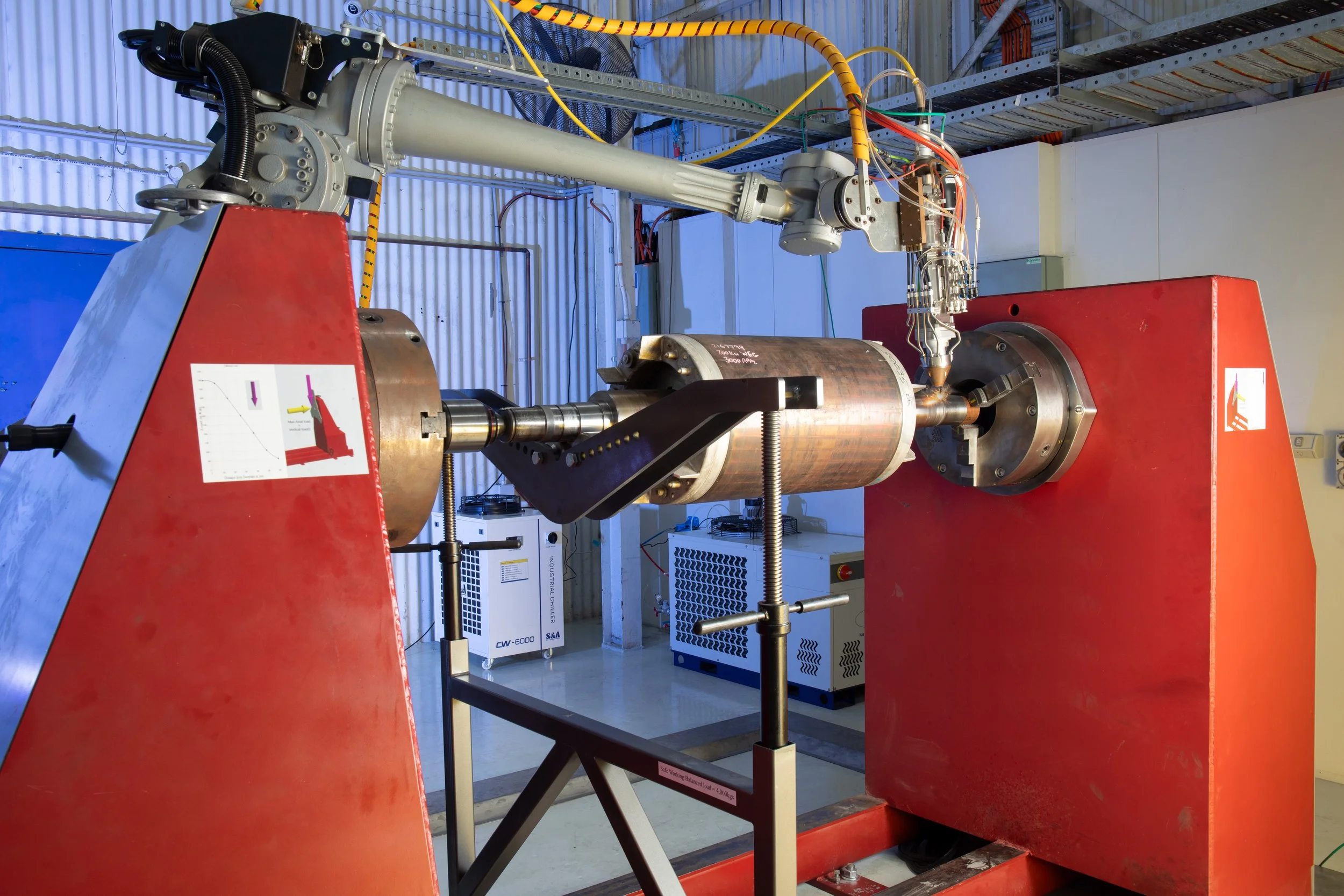
Laser Cladding
RESTORE AND FUTURE-PROOF YOUR COMPONENTS
At Australian Compressor and Engineering Services, we offer precision laser cladding services using advanced Laser Metal Deposition (LMD) technology. This cutting-edge process uses a high-powered laser to create a localized melt pool on the surface of a component, while a metallic feed material, typically a powder, is simultaneously injected and fused to the surface.
The result is a dense, metallurgically bonded coating that dramatically improves component life by enhancing wear resistance, corrosion protection, and impact performance, often all at once.
-
Coatings are applied with pinpoint accuracy, minimizing heat input and preserving the base material’s mechanical properties.
-
Fully dense coatings with no porosity, minimal dilution, and strong metallurgical bonding.
-
A wide range of powders and alloys can be applied, tailored to resist abrasion, erosion, corrosion, or impact based on your application.
-
Produces fine microstructures with enhanced strength and minimal distortion to the base material.
-
The process is fully integrated with robotic application, powder feed systems, gas shielding, and laser control—managed via an intuitive touchscreen interface for maximum process control and repeatability.
What is Laser Cladding?
Laser cladding is a modern welding-based process that deposits extremely thin layers of alloy material—sometimes as small as 0.2 mm—with exceptional precision and control. Unlike traditional deposition methods such as flame spray or arc spraying, laser cladding produces a uniform, pore-free coating with less than 5% dilution, offering superior adhesion and surface quality.
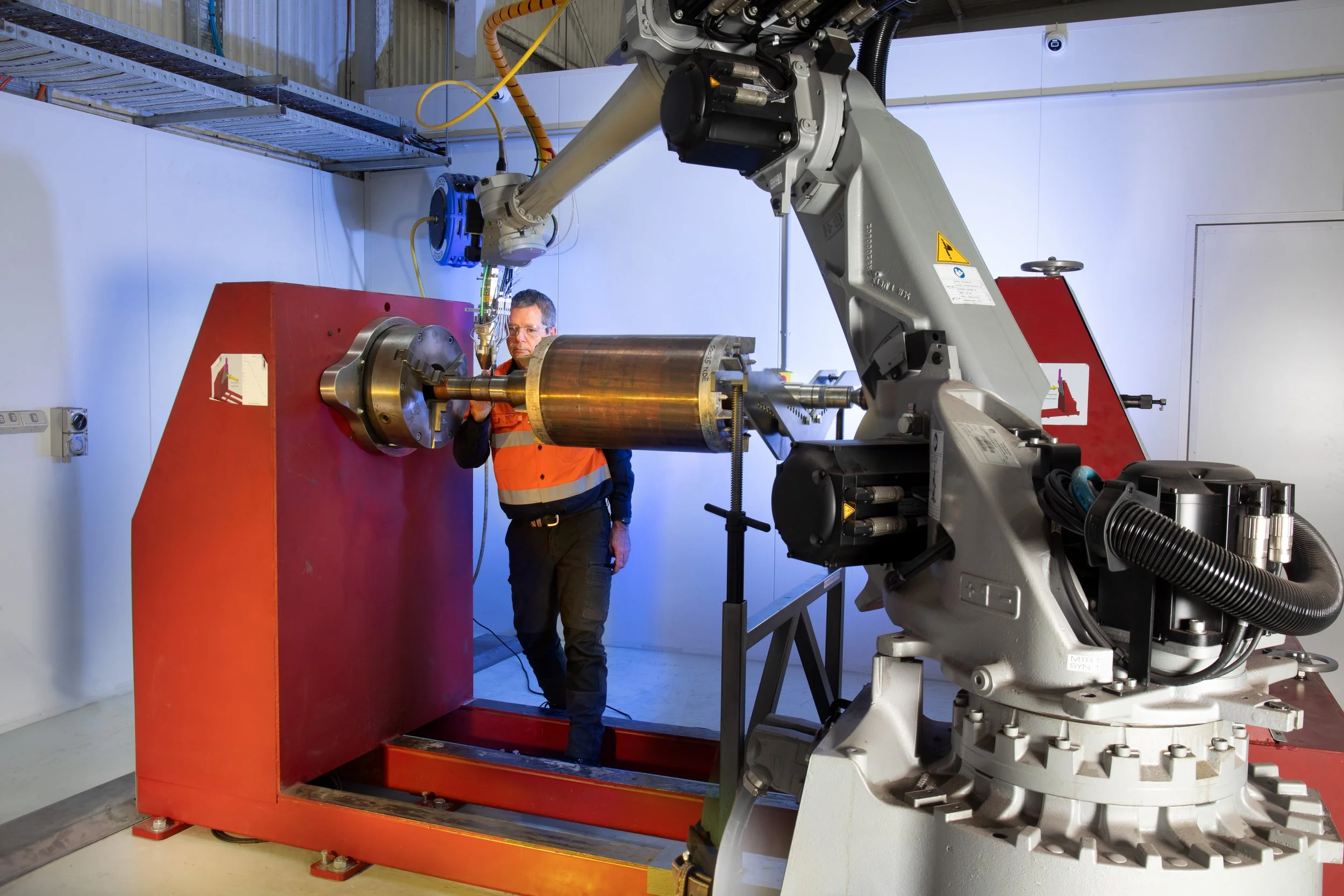
Our Services
Contact Us
If you would like to find out how Australian Compressor and Engineering Services can help you, contact our team through the form below.